Swedish Algae Factory has been cultivating a particular group of microalgae, called diatoms, and investigating their potential uses.
Diatoms are a huge group of photosynthetic microalgae that are found in almost every aquatic environment on the planet. With thousands of species, diatoms are amongst the most abundant and ecologically important microscopic organisms. They are responsible for approximately 20% of oxygen generation through photosynthesis, and can be recognised by their unique and beautifully elaborate exterior shells that contain silica.
The Swedish Algae Factory have developed a protocol for production of nanomaterials made of silica from diatoms. The extracted materials have been tested on solar panels. The naturally light trapping silica has been shown to improve the efficiency of dye – sensitised solar panels (DSSC) by as much as 60%: click here for details of their work.
The Use of Nanotechnology in Solar Energy
Oman Centre, Swedish Algae Factory partner for diatoms
Plastics are a major part of modern everyday life, recent figures estimate around 3.7 million tonnes of plastic are used per year in the UK (Plastics Europe). A proportion of the plastic is recycled after use; however, many plastic products are used once then thrown away, particularly plastic packaging. This discarded plastic does not degrade and is making its way into the oceans and waterways all over the world.
In efforts to reduce the impact of plastic pollution, biodegradable plastic has been developed, which has a shorter lifespan than conventional plastic. This type of plastic is usually made from fossil fuel feedstocks with chemical additives to enhance the degradation process. There are specific conditions to the breakdown of these plastics; high temperature and UV light; and left over products can themselves be harmful to the environment. A potential alternative is using plant based polymers to make plastics, they produce bioplastics. The difference being that bioplastics are compostable and decay into natural materials that can combine with the soil. Some of the plants used for the bioplastics are also food crops, like corn or maize, creating competition between food and plastic. Companies have been looking elsewhere for sources of materials to make plastic and one of the possibilities is algae.
Over the last few years a number of manufacturers (e.g. Solaplast; Cereplast; Bloom) and collaborative groups (e.g. SPLASH ) have been investigating and developing algal polymers. A new generation of plastic algal feedstocks is available, and being used in a variety of renewable plastic resins suitable for numerous applications.
For further developments and news on algal bioplastics and their uses – follow the links below:
Algix: http://algix.com/from-plastic-pollution-to-an-algae-solution
Vivobarefoot Sports shoes: https://www.news18.com/news/sports/your-next-shoe-could-be-made-from-algae-1447973.html and https://www.wired.com/story/slip-into-earth-friendly-running-shoes-made-of-algae/
Journal of the North Atlantic and Arctic –https://jonaa.org/content/2018/01/19/algaibioplastics
Science Daily: https://www.sciencedaily.com/releases/2013/05/130527100524.htm
Xanthella is continuing to strengthen the expertise in the ENBIO project with the recruitment of a new product engineer, Dr Laurence Evans. His role will be to oversee the design and deployment of the Pandora PBR™ array at the facility on Ardnamurchan.
Laurence is a recent PhD graduate from Heriot-Watt University, with a keen interest in microalgae and their potential in bio-based industries. His PhD examined the application of microalgae in the treatment of municipal wastewater. The aim was to establish a low-cost treatment process compared to current conventional wastewater treatment. The work focused on enhancing the ability of the microalgae to reduce nitrogenous and phosphorus concentrations through environmental and biochemical factors. Before his PhD, Laurence had completed his undergraduate degree in biochemistry at the University of Bath. During his degree, he undertook two internships, one at University College London and the second at St. Judes research hospital, located in Tennessee, USA.
As product engineer at Xanthella, Laurence has already been involved in developing a 100L volume photobioreactor to increase the product range offered by Xanthella. A number of the new Pandora 100 “Odyssey” PBRs, with customised LED light sheets, were recently delivered to the Limerick Institute of Technology in Ireland.
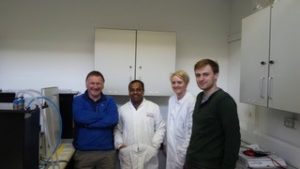